1. CENNI STORICI
La tecnologia produttiva mediante fusione a cera persa è un processo che risale all’antichità e veniva applicato alla produzione di oggetti ornamentali, di oreficeria e di statue, anche di notevoli
dimensioni; si pensi, a riguardo, ai famosi “Bronzi di Riace”. Tale tecnologia era originariamente
limitata all’impiego di metalli a basso punto di fusione, quali rame, oro, stagno e loro
leghe. Tale tecnica si è tramandata, pressoché immutata, fino ai giorni nostri, ove trova largo
impiego nelle fusioni artistiche ed orafe.
L’evoluzione tecnica ha consentito di ampliare il campo di impiego di questa tecnologia al settore
industriale sia per la produzione di particolari in serie (mediante la fusione “a grappolo”)
sia per la possibilità di utilizzo delle leghe ferrose.
La tecnologia produttiva mediante fusione a cera persa è un processo che risale all’antichità e veniva applicato alla produzione di oggetti ornamentali, di oreficeria e di statue, anche di notevoli
dimensioni; si pensi, a riguardo, ai famosi “Bronzi di Riace”. Tale tecnologia era originariamente
limitata all’impiego di metalli a basso punto di fusione, quali rame, oro, stagno e loro
leghe. Tale tecnica si è tramandata, pressoché immutata, fino ai giorni nostri, ove trova largo
impiego nelle fusioni artistiche ed orafe.
L’evoluzione tecnica ha consentito di ampliare il campo di impiego di questa tecnologia al settore
industriale sia per la produzione di particolari in serie (mediante la fusione “a grappolo”)
sia per la possibilità di utilizzo delle leghe ferrose.
2. PROCESSO TECNOLOGICO
La necessità di produrre particolari meccanici in acciaio con geometria complessa, trova soluzione
nell’applicazione del processo di microfusione a cera persa che costituisce una valida
alternativa rispetto ad altri procedimenti tecnologici più tradizionali.
La microfusione a cera persa consente attualmente l’utilizzo di una vasta gamma di acciai, compresi
gli altolegati e gli acciai inossidabili della serie 300/400/600.
La possibilità di realizzare getti con geometrie ad elevata complessità e praticamente senza limitazione di materiale, permette di produrre, in maniera economica, i più diversi particolari destinati a numerosi settori dell’industria come ad esempio alle macchine per l’industria alimentare, alle macchine automatiche per il confezionamento e l’imbottigliamento, alle macchine tessili, a componenti idraulici, oltreché particolari ornamentali di elevata finitura estetica.
La prima parte del processo produttivo prevede l’allestimento dell’attrezzatura per la produzione
dei particolari in cera simili, nella forma, a quelli che saranno poi prodotti in metallo.
A tal fine possono seguirsi diverse strade a seconda della complessità della forma del pezzo. E’
possibile realizzare uno stampo cavo, in bronzo o in ottone o in alluminio, (ma
teriali facilmente
lavorabili alle macchine utensili), entro cui colare la cera fusa che, una volta solidificata ed
estratta dallo stampo, costituirà uno degli elementi del “grappolo”.
L’eventuale presenza di sottosquadri, rientranze o cavità, se non eccessiva, può essere risolta
mediante l’utilizzo di inserti mobili negli stampi. Per pezzi di forma complessa o che presentano
numerosi recessi, specialmente di piccole dimensioni, si ricorre dapprima alla realizzazione
di un modello in resina simile al pezzo da produrre e poi, su questo, si effettua una colata di
gomma che, una volta solidificata consente l’estrazione del modello e presenta all’interno il
calco del pezzo in cera da produrre. Talora la realizzazione dei modelli di cera non si effettua
per mezzo di stampi ma mediante incisione al laser di blocchi di cera; questa tecnica permette
di realizzare finiture estremamente accurate con una notevole definizione dei dettagli.
Il modello in cera viene costruito sulla base del disegno finale del particolare che si vuole ottenere,
attuando però opportune maggiorazioni dimensionali per tenere conto del ritiro che subirà
la cera all’atto della solidificazione e delle variazioni dimensionali del materiale metallico
che costituirà il pezzo finito.
A causa delle caratteristiche bassofondenti della cera, della sua scarsa aggressività e della
modesta azione erosiva che esercita, gli stampi destinati alla realizzazione dei modelli possono
essere ottenuti con materiali a basso punto di fusione, quali ottone alluminio e bronzo, e dalle
caratteristiche meccaniche modeste. Questo comporta che la vita degli stampi, poco soggetti ad
usura, sia relativamente lunga ed inoltre l’impiego di materiali ad elevata lavorabilità meccanica
abbassano ulteriormente il costo delle attrezzature di produzione.
Il limitato costo di attrezzatura rende il procedimento conveniente anche per serie poco
numerose.
Le fasi occorrenti per costruire il getto in acciaio si svolgono secondo i seguenti punti:
1. Si ricavano i particolari in cera per mezzo di presse ad iniezione, utilizzando il relativo stampo,
o per fusione a gravità o con la modellazione al laser.
2. I particolari in cera ottenuti in serie vengono saldati assieme al colatoio e a canali di alimentazione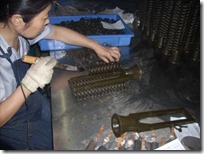
per formare il grappolo che è inizialmente tutto in cera.
3. Successivamente, una volta formato il grappolo, esso viene immerso in vasche contenenti un
impasto di silice colloidale che ha anche lo scopo di favorire il distacco del metallo dal refrattario
4. In seguito ha luogo il rivestimento per spruzzatura di materiale refrattario in polvere.
5. Queste operazioni vengono ripetute più volte, impiegando polvere a base di quarzo a granulometria crescente, fino ad ottenere un rivestimento di refrattario dello spessore voluto e
della necessaria consistenza.
6. Si provvede poi alla eliminazione della cera per semplice riscaldamento (evacuazione); in
questa fase il refrattario, che ha al suo interno il calco in negativo dei pezzi da produrre, non
ha ancora una consistenza tale da poter sopportare la spinta metallostatica del metallo fuso
e, per sopperire a ciò, viene messo in forni di preriscaldamento ad alta temperatura (circa
1000 C°) dove subisce un processo di vetrificazione.
7. Contemporaneamente, con appositi forni fusori, il metallo viene fuso e portato alla temperatura
richiesta per essere colato, a gravità. negli stampi di refrattario.
8. Avvenuta la solidificazione, il grappolo di metallo viene estratto dal suo rivestimento con
sistemi manuali a percussione che sgretolano e spaccano il rivestimento d
i terra refrattaria.
L’operazione si conclude con l’impiego di macchine sabbiatrici che puliscono il pezzo da ogni
residuo di terra.
9. Vengono a questo punto tagliati i canali di alimentazione e le diverse materozze, liberando
così i particolari in acciaio.
La necessità di produrre particolari meccanici in acciaio con geometria complessa, trova soluzione
nell’applicazione del processo di microfusione a cera persa che costituisce una valida
alternativa rispetto ad altri procedimenti tecnologici più tradizionali.
La microfusione a cera persa consente attualmente l’utilizzo di una vasta gamma di acciai, compresi
gli altolegati e gli acciai inossidabili della serie 300/400/600.
La possibilità di realizzare getti con geometrie ad elevata complessità e praticamente senza limitazione di materiale, permette di produrre, in maniera economica, i più diversi particolari destinati a numerosi settori dell’industria come ad esempio alle macchine per l’industria alimentare, alle macchine automatiche per il confezionamento e l’imbottigliamento, alle macchine tessili, a componenti idraulici, oltreché particolari ornamentali di elevata finitura estetica.
La prima parte del processo produttivo prevede l’allestimento dell’attrezzatura per la produzione
dei particolari in cera simili, nella forma, a quelli che saranno poi prodotti in metallo.
A tal fine possono seguirsi diverse strade a seconda della complessità della forma del pezzo. E’
possibile realizzare uno stampo cavo, in bronzo o in ottone o in alluminio, (ma
lavorabili alle macchine utensili), entro cui colare la cera fusa che, una volta solidificata ed
estratta dallo stampo, costituirà uno degli elementi del “grappolo”.
L’eventuale presenza di sottosquadri, rientranze o cavità, se non eccessiva, può essere risolta
mediante l’utilizzo di inserti mobili negli stampi. Per pezzi di forma complessa o che presentano
numerosi recessi, specialmente di piccole dimensioni, si ricorre dapprima alla realizzazione
di un modello in resina simile al pezzo da produrre e poi, su questo, si effettua una colata di
gomma che, una volta solidificata consente l’estrazione del modello e presenta all’interno il
calco del pezzo in cera da produrre. Talora la realizzazione dei modelli di cera non si effettua
per mezzo di stampi ma mediante incisione al laser di blocchi di cera; questa tecnica permette
di realizzare finiture estremamente accurate con una notevole definizione dei dettagli.
Il modello in cera viene costruito sulla base del disegno finale del particolare che si vuole ottenere,
attuando però opportune maggiorazioni dimensionali per tenere conto del ritiro che subirà
la cera all’atto della solidificazione e delle variazioni dimensionali del materiale metallico
che costituirà il pezzo finito.
A causa delle caratteristiche bassofondenti della cera, della sua scarsa aggressività e della
modesta azione erosiva che esercita, gli stampi destinati alla realizzazione dei modelli possono
essere ottenuti con materiali a basso punto di fusione, quali ottone alluminio e bronzo, e dalle
caratteristiche meccaniche modeste. Questo comporta che la vita degli stampi, poco soggetti ad
usura, sia relativamente lunga ed inoltre l’impiego di materiali ad elevata lavorabilità meccanica
abbassano ulteriormente il costo delle attrezzature di produzione.
Il limitato costo di attrezzatura rende il procedimento conveniente anche per serie poco
numerose.
Le fasi occorrenti per costruire il getto in acciaio si svolgono secondo i seguenti punti:
1. Si ricavano i particolari in cera per mezzo di presse ad iniezione, utilizzando il relativo stampo,
o per fusione a gravità o con la modellazione al laser.
2. I particolari in cera ottenuti in serie vengono saldati assieme al colatoio e a canali di alimentazione
per formare il grappolo che è inizialmente tutto in cera.
3. Successivamente, una volta formato il grappolo, esso viene immerso in vasche contenenti un
impasto di silice colloidale che ha anche lo scopo di favorire il distacco del metallo dal refrattario
4. In seguito ha luogo il rivestimento per spruzzatura di materiale refrattario in polvere.
5. Queste operazioni vengono ripetute più volte, impiegando polvere a base di quarzo a granulometria crescente, fino ad ottenere un rivestimento di refrattario dello spessore voluto e
della necessaria consistenza.
6. Si provvede poi alla eliminazione della cera per semplice riscaldamento (evacuazione); in
questa fase il refrattario, che ha al suo interno il calco in negativo dei pezzi da produrre, non
ha ancora una consistenza tale da poter sopportare la spinta metallostatica del metallo fuso
e, per sopperire a ciò, viene messo in forni di preriscaldamento ad alta temperatura (circa
1000 C°) dove subisce un processo di vetrificazione.
7. Contemporaneamente, con appositi forni fusori, il metallo viene fuso e portato alla temperatura
richiesta per essere colato, a gravità. negli stampi di refrattario.
8. Avvenuta la solidificazione, il grappolo di metallo viene estratto dal suo rivestimento con
sistemi manuali a percussione che sgretolano e spaccano il rivestimento d
L’operazione si conclude con l’impiego di macchine sabbiatrici che puliscono il pezzo da ogni
residuo di terra.
9. Vengono a questo punto tagliati i canali di alimentazione e le diverse materozze, liberando
così i particolari in acciaio.
3. VANTAGGI DELLA TECNICA
La microfusione di precisione, permette al progettista di ottenere ottimi risultati tecnici e di
realizzare le forme più diverse.
L’uso di getti in acciaio di precisione, oltre a garantire una consistente riduzione dei tempi di
lavorazione e quindi dei costi rispetto alle lavorazioni tradizionali, consente oggi l’ottenimento
di particolari di forma complessa praticamente nella forma definitiva e con costi di produzione
relativamente contenuti.
Vengono pertanto eliminate o ridotte al minimo le lavorazioni successive di finitura.
Per ottenere i risultati migliori è necessario seguire i concetti base della fonderia, quali evitare
gli spigoli vivi e le superfici piane ed estremamente ampie; è preferibile eventualmente ricavare
delle nervature. Queste, in genere, oltre a mantenere inalterata quella che è la rigidità del pezzo,
lo rendono più leggero, risolvendo in alcuni casi il problema del peso. Sono inoltre da evitare
forti ingrossamenti di sezione, in modo da mantenere gli spessori il più uniformi possibili. Sono
consigliabili ampi raggi di raccordo nell’incontro tra le superfici inclinate e perpendicolari.
Gli spessori minimi (circa 1,5 mm.) si possono ottenere su materiale di ottima colabilità o per
superfici estremamente limitate. Nella norma gli spessori minimi che si possono realizzare sono
di 2,5 mm. Inoltre è consigliabile avere le pareti con spessori uniformi e predisporre gli attacchi
di colata su superfici piane nella parte più grossa del getto, in modo da poter avere un’alimentazione appropriata.
I fori devono avere un diametro minimo pari ai 2/3 dello spessore della parete. Si possono ottenere
fori di un diametro minimo di 3 mm.
Sono sconsigliabili i fori ciechi. Se i fori richiedono tolleranze ristrette, si dovrà prevedere il
sovrametallo di lavorazione; fori lunghi è bene scomporli creando degli spazi; in questo modo
non si ricorrerà all’impiego di anime ceramiche.
Il peso ideale dei getti fusi a cera persa è, di norma, da pochi grammi fino a 700-800 grammi;
con questo non è preclusa però la fattibilità di getti di peso superiore.
Grazie alla possibilità di impiego di leghe ferrose come acciai al carbonio bassolegati o altolegati,
acciai inox serie 300 e 400, indurenti per precipitazioni, indeformabili da utensili, da valvole,
superleghe a base Nichel e Cobalto, il progettista è in grado di scegliere la lega più adatta,
aumentando così la qualità meccanica del getto.
La quantità richiesta non è un fattore determinante; la fusione a cera persa può essere conveniente
anche per piccole serie, bisogna però saper valutare tutte le componenti che concorrono
al prezzo finale, quali la costruzione dei modelli e della relativa attrezzatura.
Il getto fuso a cera persa ha una rugosità superficiale variabile di 3÷5 micron, a seconda del
tipo di materiale che viene impiegato.
La microfusione di precisione, permette al progettista di ottenere ottimi risultati tecnici e di
realizzare le forme più diverse.
L’uso di getti in acciaio di precisione, oltre a garantire una consistente riduzione dei tempi di
lavorazione e quindi dei costi rispetto alle lavorazioni tradizionali, consente oggi l’ottenimento
di particolari di forma complessa praticamente nella forma definitiva e con costi di produzione
relativamente contenuti.
Vengono pertanto eliminate o ridotte al minimo le lavorazioni successive di finitura.
Per ottenere i risultati migliori è necessario seguire i concetti base della fonderia, quali evitare
gli spigoli vivi e le superfici piane ed estremamente ampie; è preferibile eventualmente ricavare
delle nervature. Queste, in genere, oltre a mantenere inalterata quella che è la rigidità del pezzo,
lo rendono più leggero, risolvendo in alcuni casi il problema del peso. Sono inoltre da evitare
forti ingrossamenti di sezione, in modo da mantenere gli spessori il più uniformi possibili. Sono
consigliabili ampi raggi di raccordo nell’incontro tra le superfici inclinate e perpendicolari.
Gli spessori minimi (circa 1,5 mm.) si possono ottenere su materiale di ottima colabilità o per
superfici estremamente limitate. Nella norma gli spessori minimi che si possono realizzare sono
di 2,5 mm. Inoltre è consigliabile avere le pareti con spessori uniformi e predisporre gli attacchi
di colata su superfici piane nella parte più grossa del getto, in modo da poter avere un’alimentazione appropriata.
I fori devono avere un diametro minimo pari ai 2/3 dello spessore della parete. Si possono ottenere
fori di un diametro minimo di 3 mm.
Sono sconsigliabili i fori ciechi. Se i fori richiedono tolleranze ristrette, si dovrà prevedere il
sovrametallo di lavorazione; fori lunghi è bene scomporli creando degli spazi; in questo modo
non si ricorrerà all’impiego di anime ceramiche.
Il peso ideale dei getti fusi a cera persa è, di norma, da pochi grammi fino a 700-800 grammi;
con questo non è preclusa però la fattibilità di getti di peso superiore.
Grazie alla possibilità di impiego di leghe ferrose come acciai al carbonio bassolegati o altolegati,
acciai inox serie 300 e 400, indurenti per precipitazioni, indeformabili da utensili, da valvole,
superleghe a base Nichel e Cobalto, il progettista è in grado di scegliere la lega più adatta,
aumentando così la qualità meccanica del getto.
La quantità richiesta non è un fattore determinante; la fusione a cera persa può essere conveniente
anche per piccole serie, bisogna però saper valutare tutte le componenti che concorrono
al prezzo finale, quali la costruzione dei modelli e della relativa attrezzatura.
Il getto fuso a cera persa ha una rugosità superficiale variabile di 3÷5 micron, a seconda del
tipo di materiale che viene impiegato.
4. LAVORAZIONI SUCCESSIVE E CONTROLLI
Altre fasi successive dei cicli appena descritti sono quelle che prevedono:
• un trattamento termico con successivo controllo micrografico e di durezza
• un’analisi chimica
• una serie di controlli dimensionali.
Il trattamento termico può influenzare notevolmente le caratteristiche finali dei getti e proprio
per questo motivo, in genere, viene eseguito in atmosfera controllata con impianti fortemente
automatizzati e con gestione computerizzata dei parametri di trattamento che garantiscono la
completa ripetitività delle operazioni.
Il trattamento termico è soprattutto finalizzato a garantire l’assenza di decarburazione superficiale.
L’analisi chimica del getto può essere eseguita tramite uno spettrometro a scintilla adatto a
determinare la composizione chimica degli elementi solidi in campioni conduttivi.
Una scintilla ad alta tensione, unidirezionale, eccita e fa evaporare una porzione di materiale
di cui occorre determinare la composizione.
La scintilla avviene tra il campione e un elettrodo di tungsteno. La luce emessa da questo processo
contiene le radiazioni dei vari elementi presenti nel materiale da analizzare.
L’intensità di luce per ogni linea spettrale è proporzionale alla concentrazione dell’elemento che
l’ha prodotta.
Scopo dello spettrometro è separare e selezionare le diverse linee spettrali che devono essere
analizzate e quantificate.
A valle di tutte le operazioni sin qui descritte viene eseguito un controllo dimensionale per verificare
che il pezzo prodotto abbia le specifiche richieste dal cliente.
Altre fasi successive dei cicli appena descritti sono quelle che prevedono:
• un trattamento termico con successivo controllo micrografico e di durezza
• un’analisi chimica
• una serie di controlli dimensionali.
Il trattamento termico può influenzare notevolmente le caratteristiche finali dei getti e proprio
per questo motivo, in genere, viene eseguito in atmosfera controllata con impianti fortemente
automatizzati e con gestione computerizzata dei parametri di trattamento che garantiscono la
completa ripetitività delle operazioni.
Il trattamento termico è soprattutto finalizzato a garantire l’assenza di decarburazione superficiale.
L’analisi chimica del getto può essere eseguita tramite uno spettrometro a scintilla adatto a
determinare la composizione chimica degli elementi solidi in campioni conduttivi.
Una scintilla ad alta tensione, unidirezionale, eccita e fa evaporare una porzione di materiale
di cui occorre determinare la composizione.
La scintilla avviene tra il campione e un elettrodo di tungsteno. La luce emessa da questo processo
contiene le radiazioni dei vari elementi presenti nel materiale da analizzare.
L’intensità di luce per ogni linea spettrale è proporzionale alla concentrazione dell’elemento che
l’ha prodotta.
Scopo dello spettrometro è separare e selezionare le diverse linee spettrali che devono essere
analizzate e quantificate.
A valle di tutte le operazioni sin qui descritte viene eseguito un controllo dimensionale per verificare
che il pezzo prodotto abbia le specifiche richieste dal cliente.